Industry Insights
In the chain development of the food and beverage industry, traditional ingredient supply chains have brought numerous challenges. Previously complex, lengthy, and unregulated procurement and handover processes have become relatively fragile for many restaurant enterprises, unable to withstand challenges. This weakness has become even more apparent during the current phase of recurring pandemic outbreaks.
Therefore, achieving end-to-end management of ingredients from procurement to storefront through on-demand purchasing, reducing procurement costs, and ensuring food quality, while optimizing internal business processes to “simplify” the supply chain and enhancing digital supply chain management capabilities to boost competitiveness, has become a necessary path for the development and upgrading of chain restaurant brands.
Client Introduction
Originating in Japan, Yoshinoya has over 2,000 locations worldwide. For more than 110 years since its establishment, Yoshinoya has adhered to its mission of providing customers with food and service that is “delicious, fast, and affordable.” Shenzhen Yoshinoya Fast Food Co., Ltd. operates Yoshinoya in Guangdong Province, where it has opened nearly 50 locations. Its signature beef bowl is made from premium beef cooked with a special broth and served with steaming quality rice, earning widespread acclaim in Shenzhen.
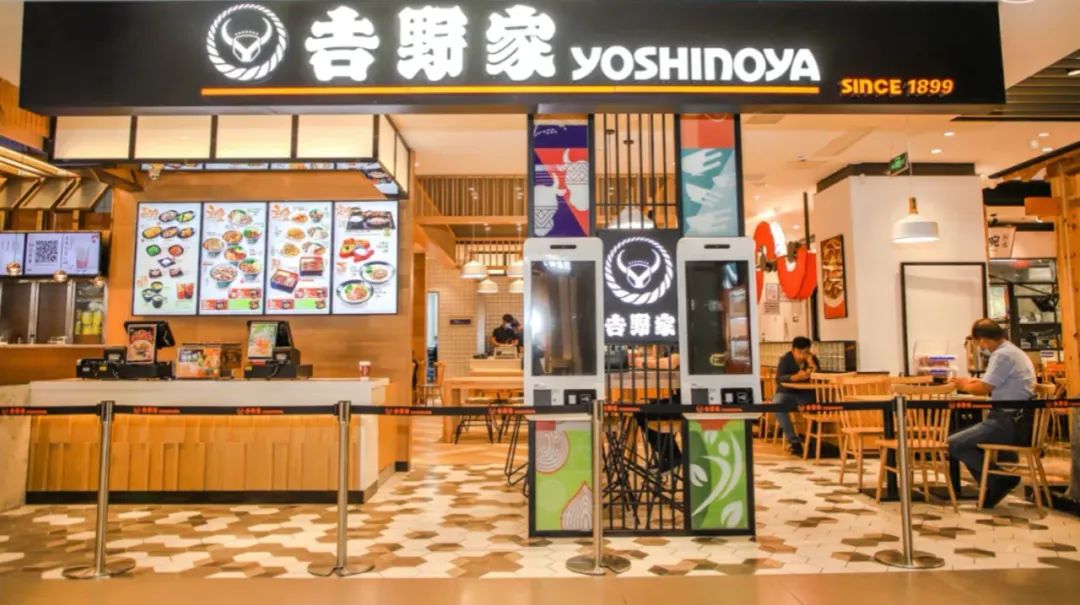
Digital Transformation Needs
1► Traditional manual ordering is inefficient and prone to errors.
Before implementing Kingdee Cloud Stellar, Shenzhen Yoshinoya stores used manual Excel spreadsheets to order ingredients, with more than 50 types of ingredients needing to be ordered daily. Store managers would compile the required ingredients and send them to the purchasing department and central kitchen, with the data then relayed to headquarters. This process resulted in low efficiency in order reception at headquarters, increased the likelihood of errors, and heightened the risk of arbitrary changes to plans.
2► Inventory management is challenging and urgently requires improved turnover efficiency
Traditional supply chains are characterized by being lengthy, sequential, and involving multiple nodes. These traits result in slow response times, an increased risk of supply chain disruptions due to sequential dependencies, and issues like information asymmetry caused by multiple nodes. For example, more than 500 types of ingredients need to be managed, each requiring different storage conditions. Yoshinoya urgently needs to establish an integrated data management platform to centrally oversee the daily inventory flow, production, and distribution data for all ingredients. This would enable the digital collaboration of supply chain management, warehouse logistics, and store sales under a unified network.
Solution
1► Digitalized store ordering significantly improves operational efficiency.
After implementing the integrated solution of Kingdee Cloud Stellar and Yi Dinghuo, Yoshinoya achieved digitalization and online management of store ordering. Store managers now create ingredient procurement plans by referencing historical sales data and complete orders directly via mobile devices. Orders are automatically synchronized with the Stellar inventory system, generating sales orders. Operations personnel can consolidate daily order requirements with a single click and then split orders by category and supplier to quickly arrange production and fresh ingredient procurement. This approach reduces communication costs between stores and headquarters, significantly enhancing store ordering efficiency.
2► “Digitalization + Supply Chain” strategy enables cost reduction and efficiency improvement.
Kingdee Cloud Stellar Inventory Management Cloud enables efficient management of multiple warehouses across different locations, with real-time updates on inventory data and clear visibility into the receipt and dispatch of goods. Additionally, it supports API integration with third-party warehousing systems to meet the data management needs of restaurant businesses relying on external storage. Leveraging the many-to-many assembly and disassembly features of Kingdee Cloud Stellar, Yoshinoya can repackage various products into multiple standard ingredient packages, significantly improving the production efficiency of pre-prepared meal kits.
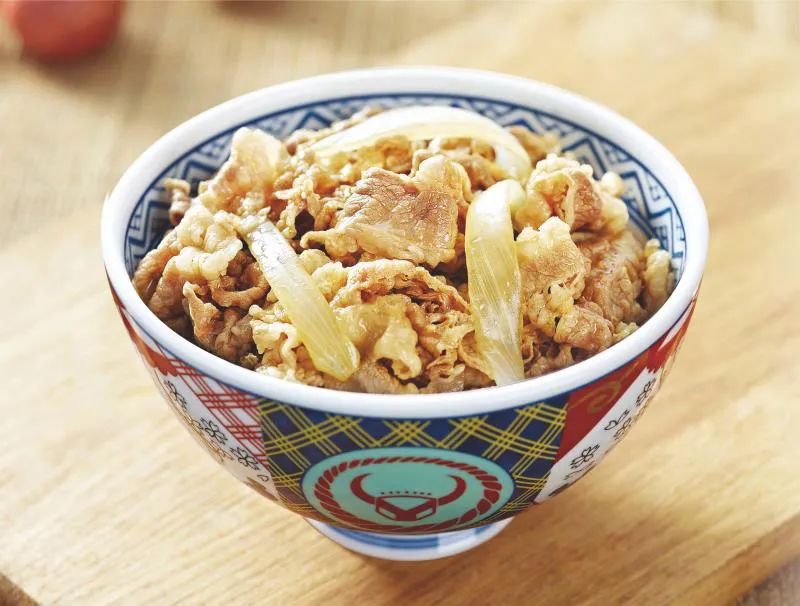