客戶概述
上海步科自動化股份有限公司(以下簡稱“步科”)專注於自動化控制核心部件和工業物聯網軟硬件產品的研發、生產與解決方案的提供。公司的自動化核心控制部件包括工業人機界面、伺服系統、步進系統、可編程邏輯控制器、變頻器等,廣泛應用於物流設備、機器人、包裝設備、食品設備、服裝設備、醫療設備、環保設備,軌道交通設備等自動化設備行業,產品遠銷海內外60多個國家。公司的工業人機界面產品市場佔有率在本土品牌廠商中多年保持領先地位。
業務挑戰
1)解決現場BOM、工藝實時性問題
在一條生產線平均1小時換線1次的生產場景下,需要在現場能根據生產訂單快速查詢到對應的BOM、工藝文件,最新的工程變更也需快速傳遞到生產現場,有效指導生產,提升效率和品質。
2)解決計劃編制不准,不及時
多品種、小批量業務場景,由於批量的降低,排產的難度同步上升,傳統手工編制方式不清楚生產的實績,計劃不准確,統計不及時,影響生產進度。需要對計劃體系進行優化,提升計劃的科學性、准確性,保障小批量多品種准時化生產。
3) 解決裝配現場物料繁雜現象
步科有物料10000余種,成品物料約3800個,常用物料約1500個,且生產以裝配為主,面對越來越多的個性化訂單,現場物料繁雜,管控困難,存在較大浪費,需要對物料進行精細化管控,降低庫存佔用,提升物料佔用率。
4) 解決現場信息流通不暢問題
通過智能終端、看板的應用實時發布生產指令,反饋生產過程數據,提升信息透明度,提高各環節協同效率。
5)現場防錯、防呆
通過物料防錯、工藝防錯、生產首檢防錯、質量漏檢防錯、設備信息監控防止生產現場的錯漏裝,提升生產品質。
6)解決現場追溯困難問題
需實現包括關鍵件、原材料、品質、WIP的實時追溯,實現從材料、檢驗、生產的全過程追溯,為產品的全生命周期維護提供保障。
解決方案
步科智慧工廠建設內容包括ERP、MES、WMS系統,並與硬件進行集成實現軟硬一體化,實現了財務、供應鏈、生產、倉儲物流的全方位標准化、智能化管控。
整體方案藍圖:
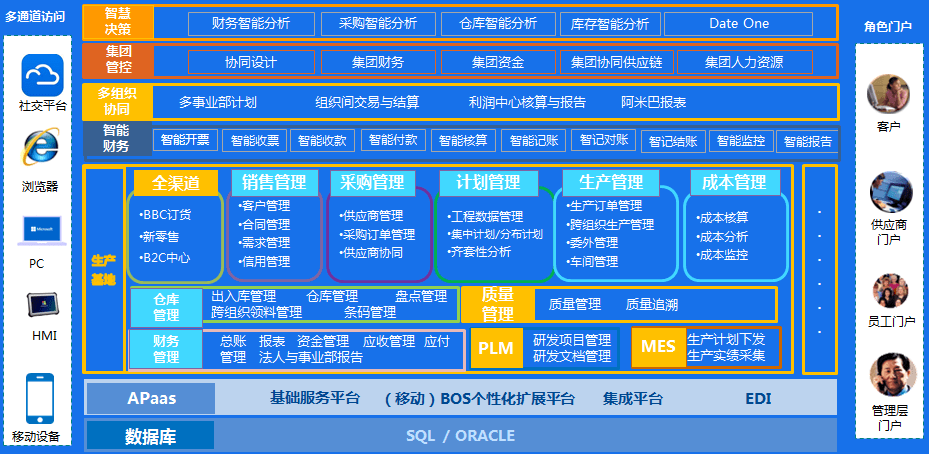
步科智慧工廠建設的核心內容如下:
(1) 產品全程感知——條碼技術應用
條碼追溯與防呆貫穿智能工廠產品生產的始終,從供應商端到產品售后維修,實現產品的全生命周期追溯,按照質量管理要求結合倉庫管理現狀,步科在條碼應用方面啟用了物料代碼、批號、追溯號、序列號等四種規則:追溯號可以用來生產追溯但出入庫時可以不記錄對應序列號,對自制成品啟用序列號單品管理,對每個序列號所耗用材料,生產過程進行記錄。
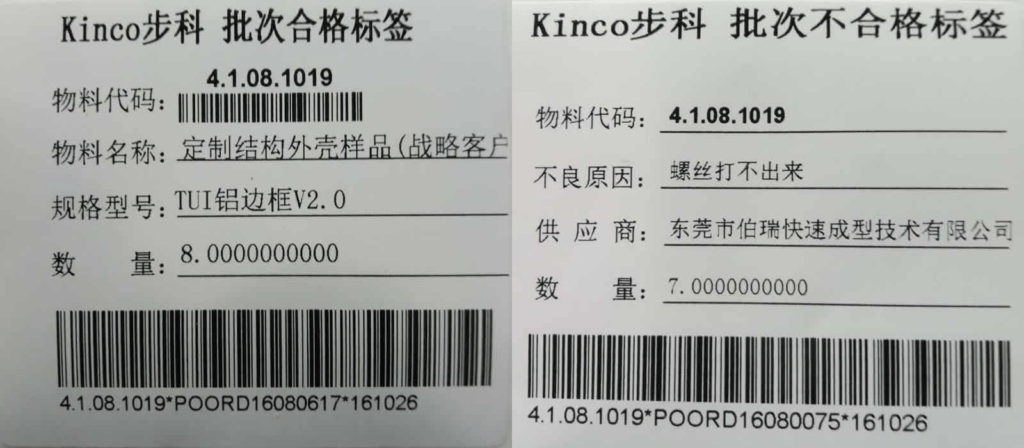
(2) 智能排程
生產訂單排程系統自動將訂單分配生產線、更新計劃訂單計劃開工時間、更新子項物料的需求時間,實現對生產線產能預警並拉動生產備料。 步科使用柔性生產功能,通過柔性產線中工作日歷,考慮柔性產線與物料關系中優先級及柔性工藝路線中工序對應作業時間,對生產訂單進行有限產能排程。
生產訂單排程讓生產系統變得有序透明,排程直接下發到生產小組,小組工作不需要再由組長安排,讓小組員工具有充分的自主性。出現異常不能得到及時處理時,員工有權利切換工單,而物流系統隨員工切換而拉動。在正常情況下,物料根據現場消耗情況,亦實現按需拉動。
(3) 生產過程數字化加強生產過程管控
生產現場使用智能終端與連接現場人員、設備,通過打通ERP與MES數據鏈路,實現數據實時下發至到工位智能終端,用戶能過智能終端進行作業。在終端上用戶能方便的進行條碼掃描、上料、報工、報警、切換工單、首檢、完工送檢、打印、查看作業指導書等操作,讓車間用戶通過智能終端就能實現所有業務。
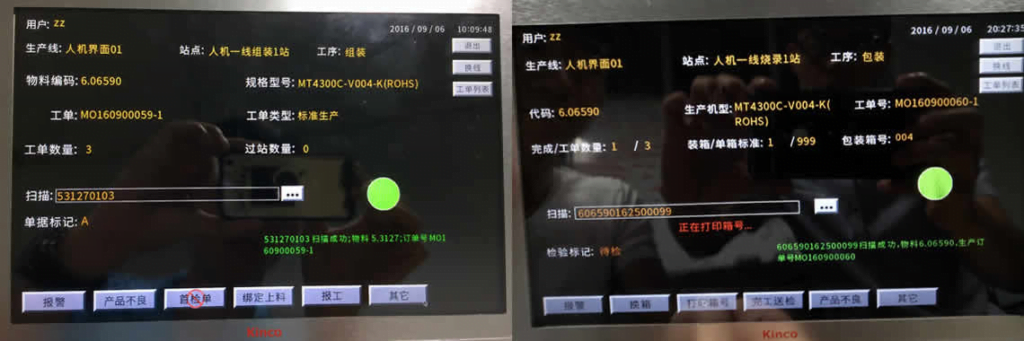
同時,通過人工採集數據與設備採集數據結合,實現工業現場人機料法環數據的有效獲取(附圖為產品老化數據的獲取)。
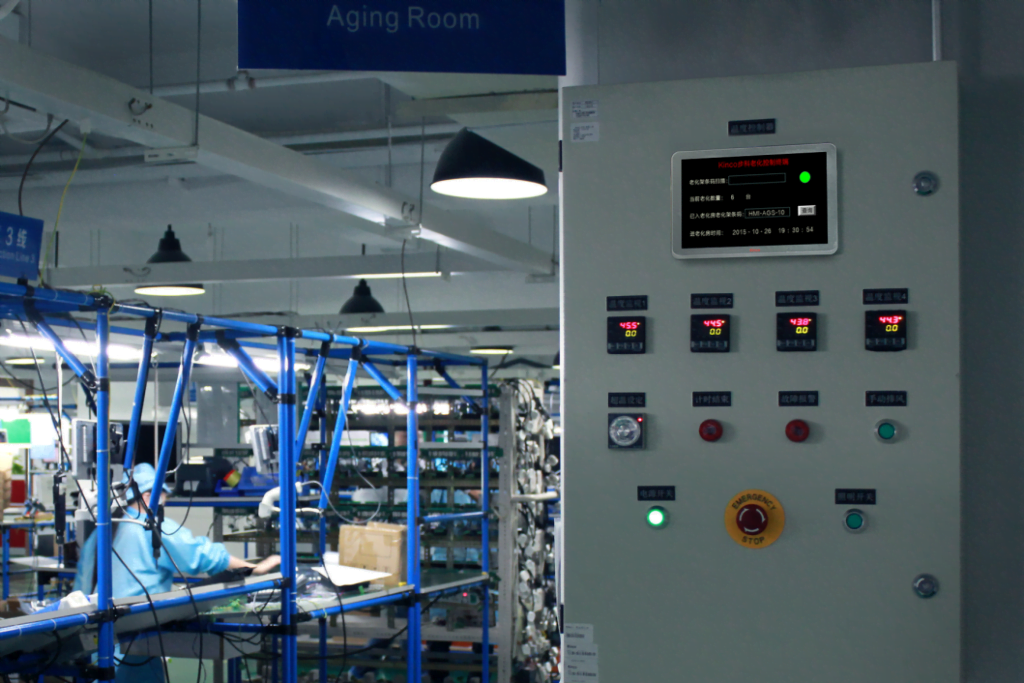
獲取的數據用於步科產品的持續改善,如生產進度數據,我們用於制造周期改善。通過過程數據採集,能夠清晰的確認到生產物流數據:倉庫什麼時間開始備料,工單什麼時間完成,成品檢驗什麼時候開始等。通過生產工序節拍數據的分析,我們很清楚的知悉,我們制造過程中間存在的問題點。未達成產能的原因。
數據亦通過智能電子看板進行實時呈現。產品實時狀態、進度等信息的多維可視化,可深入到問題的背后,找到關聯的數據信息,幫助客戶快速解決現場的異常問題。
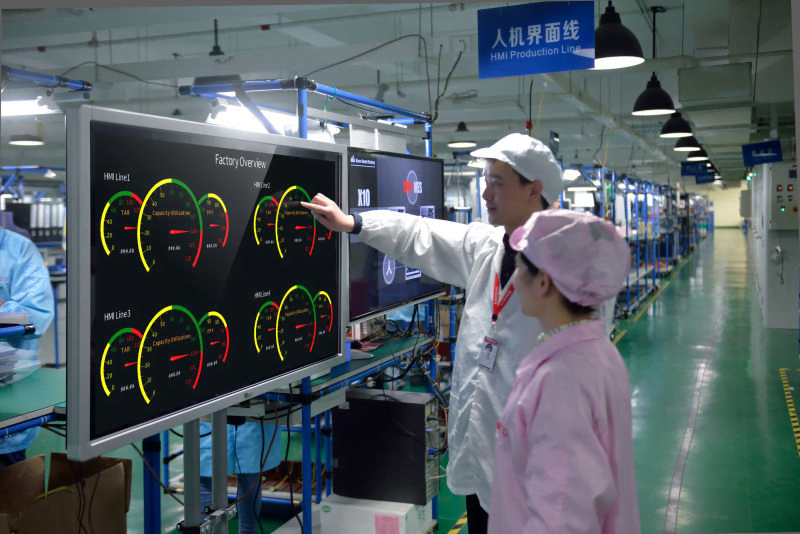
(4) 智能物流
智能物流方案,通過軟硬件的充分結合,保証物流及時性。
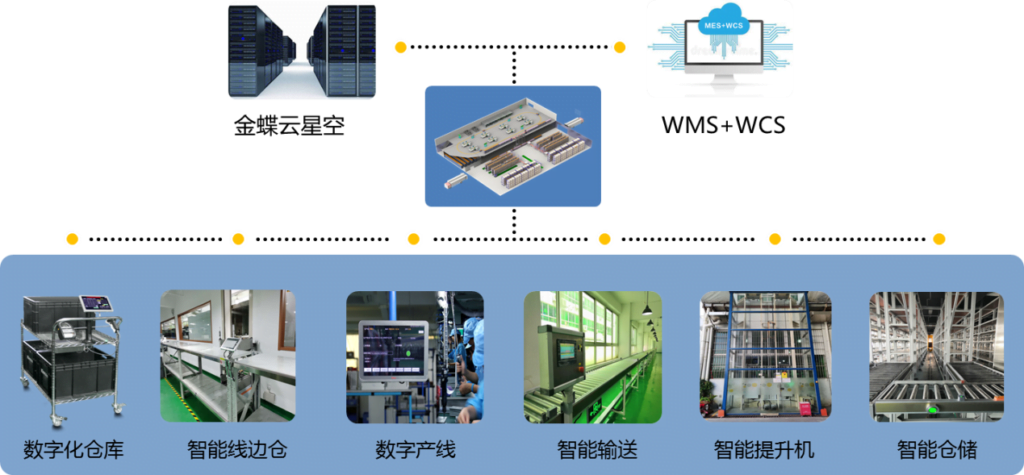
智能立體倉庫將WMS智能算法、創新的機械手設計與揀貨人員完美結合,實現人機數據的協同作業。智能立體倉庫將貨架的下面三層定義為揀貨區,上面層次定義為存貨區。機械手通過WMS智能優化算法驅動,自動進行庫位的上下調整。保証揀貨區物料滿足訂單需求。而當訂單到達倉管員的移動智能終端時,倉管員隻需要點擊觸發工單,系統會獲取到相應物料信息,在揀貨區對應庫位進行亮燈,作業人員隻需要按照亮燈的庫位依次進行揀貨。揀貨人員的效率達到最優水平。
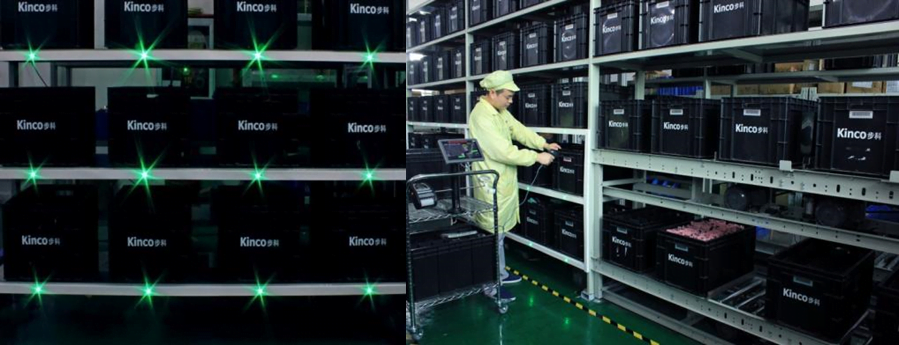
智能揀貨小車,結合多品種小批量的特點,由智能終端、條碼槍、無線模塊、移動電池;配置好WIFI后,在倉庫范圍內跟隨倉庫人員進行現場操作;生產工單下達后,需要備貨的信息傳達到揀貨小車上,根據亮燈系統的指引,實際揀貨后用條碼槍進行匯報;實現零距離、零等待的數據處理,解決庫存不准的頑疾。
基於步科的戰略要求,本次項目首先搭建了智慧工廠頂層設計方案,並配合軟硬件研發一次性的推動整體方案的落地。
1) 軟件平台建設
新一代信息技術、雲平台的應用是智能制造轉型的重要一環。以步科智慧工廠頂層設計為指導方針,步科智慧工廠首先建設了一套涵蓋ERP、MES、WMS的軟件平台,助力步科構建強有力的內部管理體系,讓其內部信息流在各個業務環節高效流轉共享,實現企業經營管理、生產執行、倉儲物流的高效協同。其中雲ERP的搭建,從財務、銷售、計劃、成本、供應鏈幾個方面實現資源優化、將流程標准化;MES系統的搭建,實現生產過程現場數字化,讓生產執行敏捷、高效、透明;WMS系統的搭建,保証物料准時化供應,提高倉儲物流效率及透明度,快速響應生產各工序的即時配送要求;並通過 ERP+MES+WMS一體應用提升其內部經營、生產的效率,優化成本管控。
2) 硬件平台構建
智慧工廠建設,軟硬一體才能讓智能制造系統發揮其最大的效能。在軟件系統建設的同時,步科發揮其自動化廠商優勢,同步進行了硬件平台的構建。為適應多品種、小批量生產模式下,現場高節拍、換線頻繁、物料種類多配送頻率高等特點,步科智慧工廠項目先后完成構建了智慧終端、數據採集網關、電子看板、智能貨架、智能RGV小車、物料輸送滾筒線等硬件設施,並將硬件設備與軟件平台進行無縫對接,實現軟件平台與硬件設備的生產聯動,生產指令實時下發至設備,執行數據實時上傳至軟件系統,並實時透明化展示。通過軟硬一體化的智慧工廠解決方案,以提升生產現場的執行效率和品質,降低整體成本。
3) 精益改善
持續優化 在數字化基礎上,結合精益管理思想,不斷對生產現場進行精益改善,發揮智慧工廠的最大作用,持續為步科的發展注入新的動力。
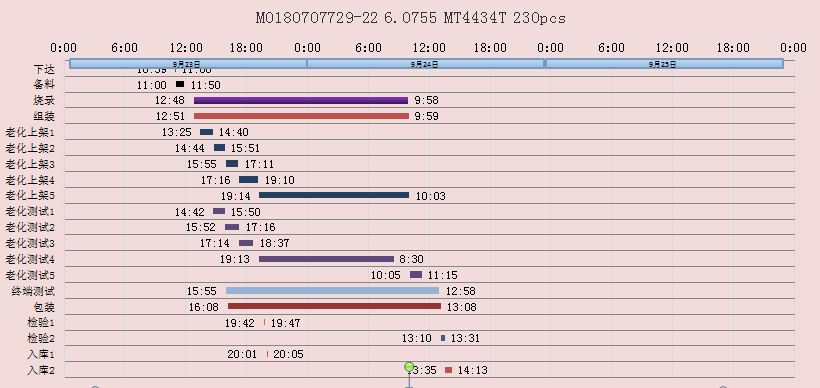
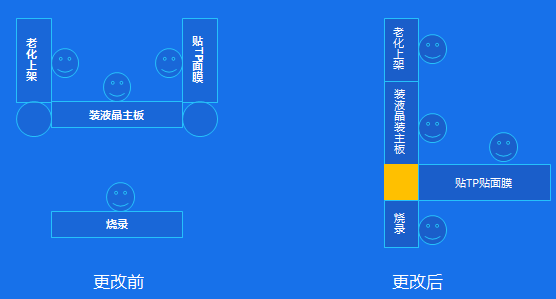
客戶價值
通過ERP+MES+WMS一體化、軟硬一體化智能管控平台的應用,實現了數據在雲端存儲,工廠全過程無紙化、可視化,工序間高效流轉,各生產組織部門高效協同,生產效率快、作業精度高,讓工廠可以和設計者、客戶、供應商在雲端數顯數據共享以及通過應用軟件實現協同,可快速響應客戶多元化的需求,真正做到多品種小批量的柔性生產制造模式。在品質、效率、交期幾個方面得到了的大幅提升。實現了換產時間0小時,生產數據0等待,生產工位0距離的三0應用,制造周期由7.67天下降到0.9天,人均產值提升81.8%。
智慧工廠結合精益改善,幫助步科消除了生產現場大量的浪費,在不增加一個人的情況下,步科實現了產值翻番。
表現在:
1. 產供銷高效協同,客戶履約得到保障
2. 庫存得到合理控制,保障生產日清日結
3. 生產數字化,實現過程精細化管控
4. 生產精益化,浪費逐漸消除,產能翻番
5. 大量節省倉儲空間,配送時間降低